Forging a Utilitarian Classic
The art of the blacksmithing returns to the Tucson Presidio.
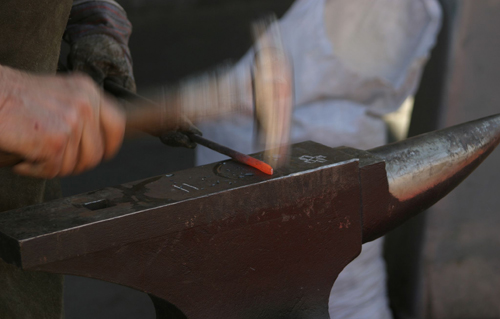
Blacksmithing is disciplined, detailed work, needing strength and dexterity to stoke the fires and hit the molten metal with the correct pressure.
Photo via Wikimedia Commons/Scott Sandars
On Nov. 9, the unmistakable scent of hot metal will waft through the Presidio San Agustín del Tucson, re-introducing the lore of the smithy to Tucson.
That day, from 10 a.m. until 4 p.m., the Arizona Artist Blacksmith Association (AABA) holds a metalworking event at Presidio San Agustín, a mix of demonstration for the public and technique-honing for the professionals. Modern-day blacksmiths will hammer away at the red ore in the reconstructed fort at the corner of Washington Street and Court Avenue, keeping tradition alive and showing crowds how frontier smithing was a cornerstone of settlement survival in Tucson.
Blacksmithing was critical to this dusty northern outpost of New Spain when the presidio fort was built in the 1780s by the conquistadors. Smiths were the armorers who repaired weapons for military and their trade also served settlers by shaping metal shoes for horses and mules, forging nails, hardware or tools for building, and repairing essential equipment, such as wagons and plows.
The AABA has conducted demos state-wide since the association’s founding in 1981, for both the public and also for the 235 state-wide members, 44 of whom are based in Southern Arizona. Although many members are hobbyists, there is a strong core of practicing blacksmiths still at work in Tucson. Two Tucson metal smiths and AABA members, Bill Ganoe and Eric Thing, helped initiate this Tucson Presidio demonstration.
Tucson’s blacksmithing legacy has roots in the 11-acre presidio downtown, probably to the west of City Hall and south of Alameda, at the site pinpointed by archaeologists as the first blacksmithing operation. In the 1850s, a ring-shaped, 1400 pound meteorite (still the largest of its kind in the world) was used as an anvil at this site. Although the Smithsonian now houses this meteorite, its replica is on display at Flandrau Science Center on UA’s campus. More modern-day Tucson smithing lore is found at 724 N. Main St., where Wm. Flores and Son, Tucson’s contemporary first family of practicing blacksmiths, has been stoking its forge since 1929. The family’s first shop was on Court Street.
Storied Hands
Blacksmithing was always hard work in the west. With new iron expensive and hard to come by, very little was produced in colonial Mexico, and iron that was shipped to settlers from across the Atlantic Ocean needed to be hauled up to New Spain by mule train from Veracruz. The Industrial Revolution sped the demise of the handcraft, and blacksmithing may have become extinct if not for the founding of the Artist Blacksmith Association of North America (ABANA) in 1973.
The AABA, a chapter of the North American organization, continues its demonstrations and workshops in an effort to document the stories and techniques of the master craft. Harold Hilborn, a Tucson blacksmiths and founder of Holy Hammer Ironworks, doesn’t want the craft to fade into history, and meticulously preserves old-style handwork as do many of his fellow association members.
“This is why we hold our demonstrations for the public, to keep the forges lit and burning, and help the craft stay alive,” says the skilled smith.
Blacksmithing is disciplined, detailed work, needing strength and dexterity to stoke the fires and hit the molten metal with the correct pressure. It’s a lifetime practice that’s also an art.
Functional Craft
According to Hilborn, blacksmiths put a little bit of themselves into each piece, while staying true to historic principles of craftsmanship and functionality.
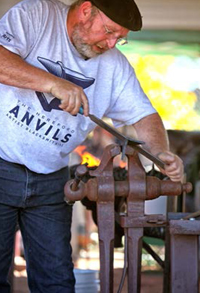
Adrian Legge at a September AABA demonstration in Camp Verde.
Photo by Barry Denton
“We take tools of and techniques of the past and use them to sculpt functional art for homes or business,” says Hilborn. For metal art admirers, Hilborn wants to clarify an often incorrectly-used term: “The metal security iron you see on homes and business is ornamental iron, not wrought iron. Wrought iron is a type of metal with very little carbon in it, and around World War II manufacture or production of it stopped, as alloy steel became more prevalent. Back in the day, ornate decorative iron was produce by a blacksmith shop but it was largely forged wrought iron bars with cast iron elements.”
Modern blacksmiths still produce this type of work today but use low-carbon steel alloys for art that ranges from railings and decorative furniture, to fireplace enclosures, sculpture and lighting. “A main difference between a modern blacksmith and a fabricator/welder is that we use a forge anvil and hammer to shape our products, to give them texture and life,” Hilborn explains.
Demo Details
The pros will get a chance to work with master craftsman Mark Aspery – certified with Worshipful Company of Blacksmiths, the UK-based guild that begun in London in 1324 – in a two-day Joinery Workshop the same weekend as the Presidio San Agustín del Tucson demo. Skills (ability to perform basic forging techniques and to hammer for several hours each day) and separate registration for the Nov. 10-11 workshop are required.
While the blacksmith demonstrations are underway on Nov. 9, onlookers also will have a chance to purchase gear and books, as well as browse a tailgate with association members selling mostly blacksmithing-related items and tools. An afternoon drawing for an “Iron-in-the-Hat” raffle (of forged art and functional items on display during the demonstrations) will benefit the AABA general fund.
Head to the Presidio San Agustín del Tucson, 133 W. Washington St., Nov. 9 to see hot metal hammered and a classically-wrought, utilitarian art. Admission to the demonstration is free to the general public, but there is $20 fee for AABA members. Donations will help benefit the Presidio rebuilding effort.
Safety goggles may be de rigueur, of course.
More details on the Nov. 9 event are at TucsonPresidio.com. For information on the Nov. 10-11 Joinery Workshop and Arizona Artist Blacksmith Association, visit AZ-Blacksmiths.org.
Also find us on...